Халуун агаарын гагнуурыг халуун агаарын гагнуур гэж нэрлэдэг. Шахсан агаар эсвэл инертийн хий (ихэвчлэн азот) нь гагнуурын буу дахь халаагуураар дамжуулан шаардлагатай температурт халааж, хуванцар гадаргуу болон гагнуурын туузан дээр цацаж, бага даралтын дор хайлуулж, нэгтгэдэг. Хүчилтөрөгчөд мэдрэмтгий хуванцар (полифталамид гэх мэт) нь халаах орчин болгон инертийн хий ашиглах ёстой бөгөөд бусад хуванцарууд нь ерөнхийдөө шүүсэн агаарыг ашиглаж болно. Энэ аргыг ихэвчлэн поливинил хлорид, полиэтилен, полипропилен, полиоксиметилен, полистирол, карбонат зэрэг хуванцарыг гагнахад ашигладаг.
Xinfa гагнуурын төхөөрөмж нь өндөр чанартай, хямд үнээр ялгаатай байдаг. Дэлгэрэнгүй мэдээллийг:Гагнуур ба зүсэх үйлдвэрлэгчид - Хятад гагнуур ба зүсэх үйлдвэр ба ханган нийлүүлэгчид (xinfatools.com)
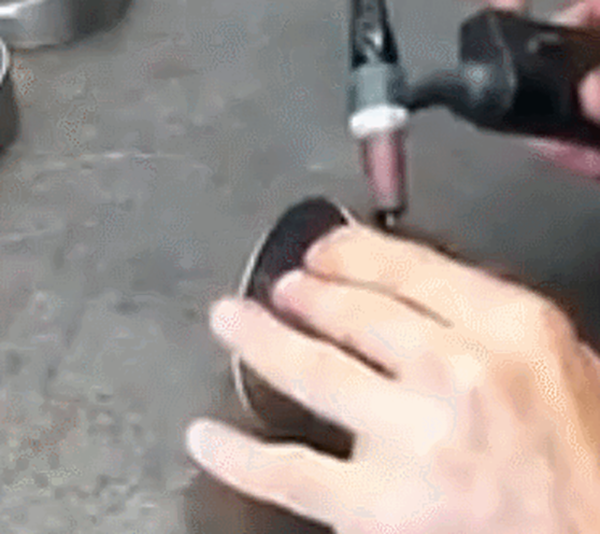
Халуун даралтын гагнуур нь металл утас болон металл гагнуурын хэсгийг хооронд нь дарахын тулд халаалт, даралтыг ашигладаг. Уг зарчим нь гагнуурын талбайн металыг халаалт, даралтаар хуванцараар деформацид оруулах ба үүнтэй зэрэгцэн даралтат гагнуурын интерфэйс дээрх ислийн давхаргыг устгаж, даралтат гагнуурын утас ба металлын хоорондох контакт гадаргуу нь атомын таталцлын хэмжээнд хүрдэг. хүрээ, ингэснээр атомуудын хооронд таталцлыг бий болгож, холболтын зорилгод хүрдэг.
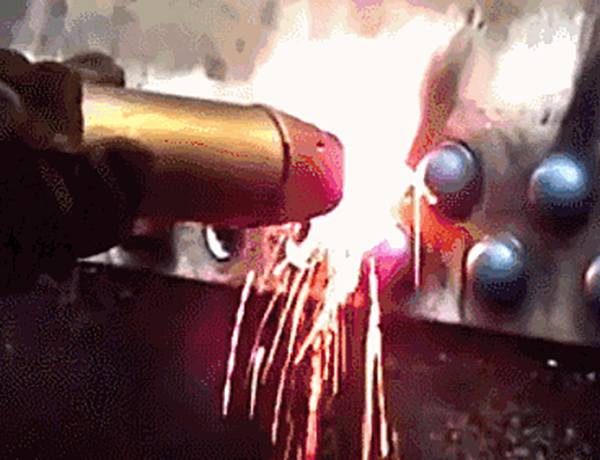
Халуун хавтан гагнуур нь хавтан зурах бүтцийг ашигладаг бөгөөд халаалтын хавтангийн машины дулааныг цахилгаан халаагуураар дээд ба доод хуванцар халаалтын хэсгүүдийн гагнуурын гадаргуу руу шилжүүлдэг. Гадаргууг хайлж, дараа нь халаалтын хавтангийн машиныг хурдан татаж авдаг. Дээд ба доод халаалтын хэсгүүдийг халаасны дараа хайлсан гадаргууг хайлуулж, хатууруулж, нэг болгон нэгтгэнэ. Бүхэл бүтэн машин нь дээд загвар, доод загвар, халуун загвар гэсэн гурван хавтангаас бүрдэх хүрээ хэлбэр бөгөөд халуун хэв, дээд ба доод хуванцар хүйтэн хэвээр тоноглогдсон бөгөөд үйл ажиллагааны горим нь пневматик удирдлага юм.
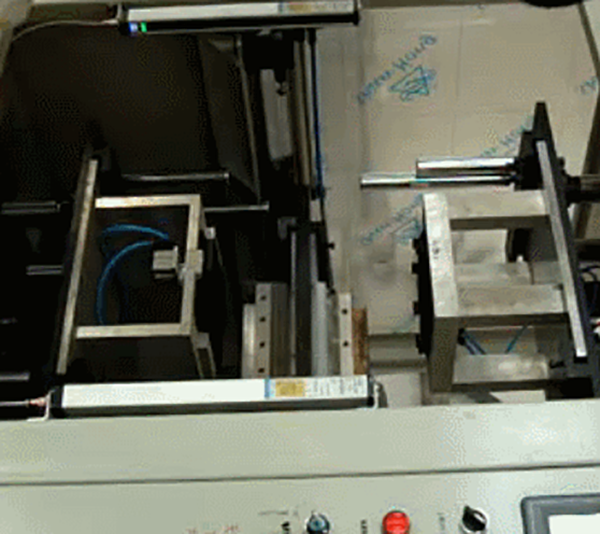
Хэт авианы металл гагнуур нь өндөр давтамжийн чичиргээний долгионыг ашиглан гагнах хоёр металл гадаргуу руу дамжуулдаг. Даралтын дор хоёр металл гадаргуу нь бие биенийхээ эсрэг үрж, молекулын давхаргын хооронд нэгдэл үүсгэдэг. Үүний давуу тал нь хурдан, эрчим хүч хэмнэх, хайлуулах өндөр бат бэх, сайн дамжуулалт, оч үүсгэдэггүй, хүйтэн боловсруулалтанд ойрхон; түүний сул тал нь гагнасан металл эд анги нь хэтэрхий зузаан (ерөнхийдөө 5 мм-ээс бага эсвэл тэнцүү), гагнуурын байрлал хэт том байж болохгүй, даралт шаарддаг.
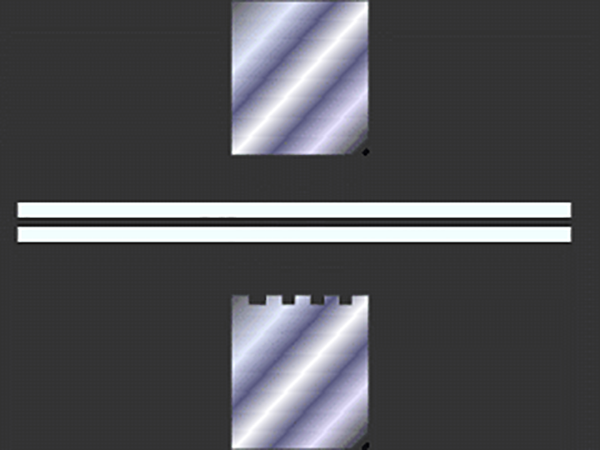
Лазер гагнуур нь өндөр эрчим хүчний нягтралтай лазер туяаг дулааны эх үүсвэр болгон ашигладаг үр ашигтай, нарийн гагнуурын арга юм. Энэ нь лазер материал боловсруулах технологийн хэрэглээний чухал талуудын нэг юм. Ерөнхийдөө тасралтгүй лазер туяа нь материалын холболтыг дуусгахад ашиглагддаг. Түүний металлургийн физик процесс нь электрон цацраг гагнууртай маш төстэй бөгөөд өөрөөр хэлбэл энерги хувиргах механизм нь "түлхүүр нүхний" бүтцээр дамждаг. Хөндий дэх тэнцвэрт температур нь ойролцоогоор 2500 ° C байх ба дулааныг өндөр температурт хөндийн гаднах хананаас шилжүүлж, хөндийг тойрсон металлыг хайлуулдаг. Түлхүүрийн нүх нь цацрагийн цацрагийн дор ханын материалын тасралтгүй ууршилтаас үүссэн өндөр температурт уураар дүүрдэг.
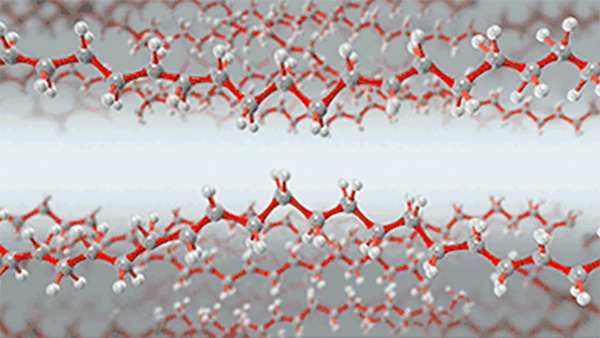
Цацраг нь түлхүүрийн нүхэнд тасралтгүй орж, нүхний гаднах материал тасралтгүй урсдаг. Цацраг хөдөлж байх үед гол нүх нь үргэлж тогтвортой урсгалтай байдаг. Хайлсан металл нь түлхүүрийн нүхийг зайлуулсны дараа үлдсэн цоорхойг дүүргэж, конденсацлаж, гагнуур үүсдэг.
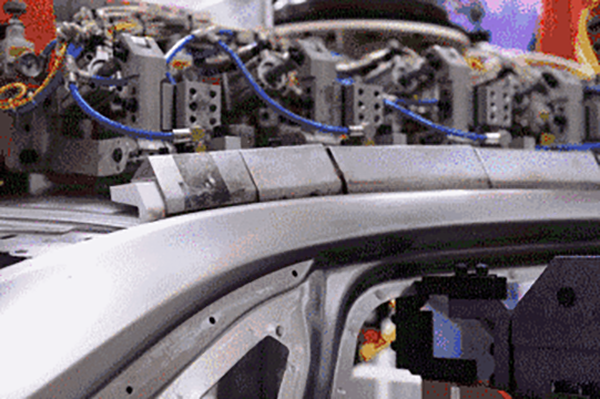
Гагнуур нь гагнуурын арга бөгөөд холбосон бэлдэцээс бага хайлах цэгтэй хайлсан дүүргэгчийг (гагнуурын материал) хайлах цэгээс дээш температурт халааж, хоёр ажлын хэсгийн хоорондох зайг капилляраар бүрэн дүүргэх хангалттай шингэн болгодог. үйлдэл (нойтон гэж нэрлэдэг), дараа нь хатуурсны дараа хоёуланг нь холбодог. Уламжлал ёсоор АНУ-д 800°F (427°C)-аас дээш температурыг brazing (хатуу гагнах), 800°F (427°C)-аас доош температурыг зөөлөн гагнуур (зөөлөн гагнуур) гэж нэрлэдэг.
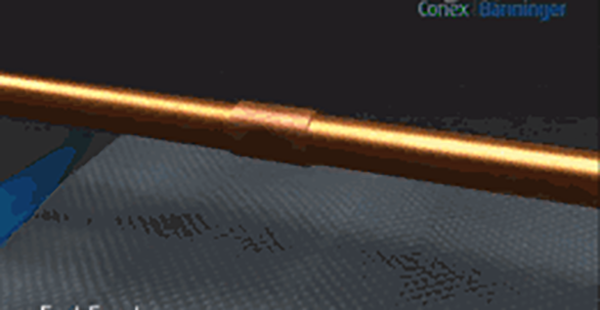
Гар гагнуур нь гар гагнуурын бамбар, гагнуурын буу эсвэл гагнуурын хавчаараар гүйцэтгэдэг гагнуурын арга юм.
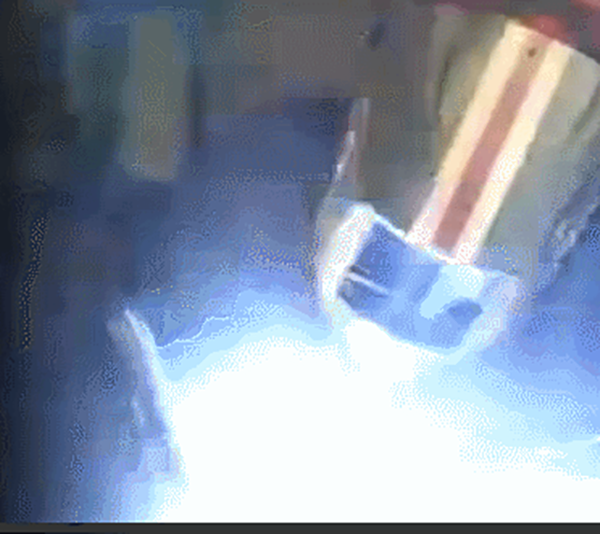
Эсэргүүцлийн гагнуур нь металл эсвэл хуванцар гэх мэт бусад термопластик материалыг халаахад ашигладаг үйлдвэрлэлийн процесс ба технологи юм. Энэ нь бэлдэцийг угсарсны дараа электродоор дарж, үений контактын гадаргуу болон зэргэлдээх хэсгүүдээр дамжин өнгөрөх гүйдлийн эсэргүүцлийн дулааныг ашиглан гагнах арга юм.
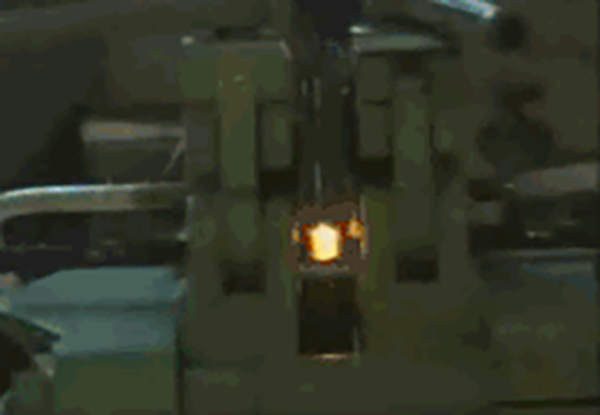
Үрэлтийн гагнуур нь механик энергийг эрчим хүч болгон ашигладаг хатуу фазын гагнуурын арга юм. Энэ нь ажлын хэсгүүдийн төгсгөлийн гадаргуугийн хоорондох үрэлтийн үр дүнд үүссэн дулааныг хуванцар төлөвт хүргэхийн тулд ашигладаг бөгөөд дараа нь гагнуурыг дуусгахын тулд дээд хуурамчаар хийдэг.
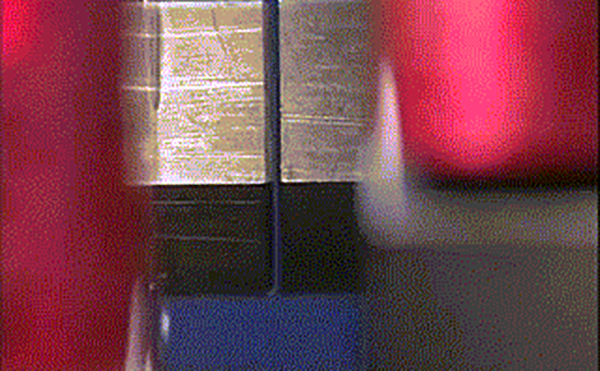
Электрослаг гагнуур нь шаарыг дамжин өнгөрөх гүйдлийн улмаас үүссэн эсэргүүцлийн дулааныг дүүргэгч металл болон үндсэн материалыг хайлуулах дулааны эх үүсвэр болгон ашигладаг бөгөөд хатуурсны дараа металлын атомуудын хооронд хүчтэй холбоо үүсдэг. Гагнуурын эхэн үед гагнуурын утас болон гагнуурын ховил нь нумыг эхлүүлэхийн тулд богино холболттой бөгөөд бага хэмжээний хатуу урсгалыг тасралтгүй нэмнэ. Нумын дулааныг хайлуулж шингэн шаар үүсгэдэг. Шаар тодорхой гүнд хүрэхэд гагнуурын утсыг тэжээх хурд нэмэгдэж, хүчдэл багасдаг тул гагнуурын утсыг шаарны санд оруулж, нумыг унтрааж, цахилгаан гагнуурын процессыг идэвхжүүлдэг. Цахилгаан гагнуур нь голчлон хайлах хошууны электрошлаг гагнуур, хайлдаггүй хошууны цахилгаан гагнуур, утсан электродын цахилгаан гагнуур, хавтан электродын электрошлаг гагнуур г.м. Үүний сул тал нь оролтын дулаан их, үе нь өндөр температурт удаан байдаг, гагнуурыг хэт халахад хялбар, гагнуурын метал нь том ширхэгтэй талст цутгамал бүтэцтэй, цохилтын бат бөх чанар бага, гагнуурын дараа гагнуурыг ерөнхийд нь хэвийн болгож, хатууруулах шаардлагатай.
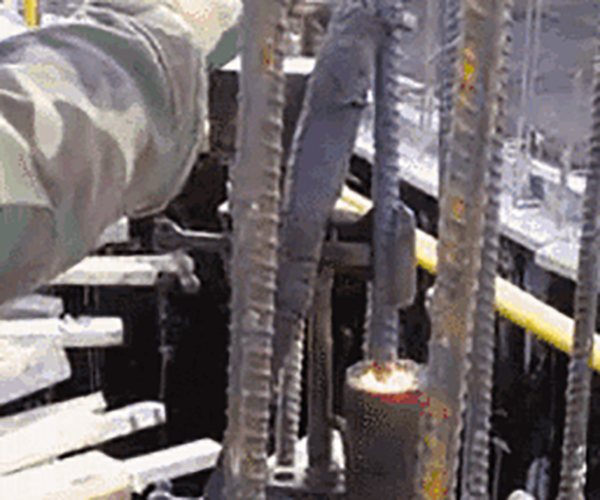
Өндөр давтамжийн гагнуур нь хатуу эсэргүүцлийн дулааныг эрчим хүч болгон ашигладаг. Гагнуурын явцад ажлын хэсэг дэх өндөр давтамжийн гүйдлийн улмаас үүссэн эсэргүүцлийн дулааныг ажлын хэсгийн гагнуурын талбайн гадаргууг хайлсан эсвэл бараг хуванцар төлөвт халаахад ашигладаг бөгөөд дараа нь (эсвэл үгүй) металлын холболтыг бий болгохын тулд эвдрэх хүчийг хэрэглэнэ.
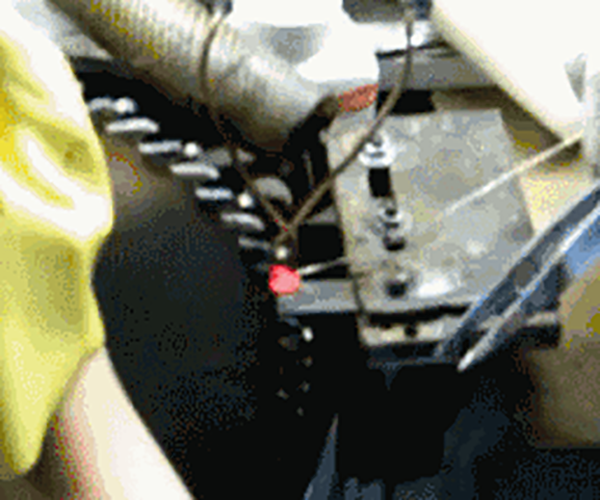
Халуун хайлмал нь эд ангиудыг (шингэн) хайлах цэг хүртэл халаах замаар хийгддэг холболтын төрөл юм.
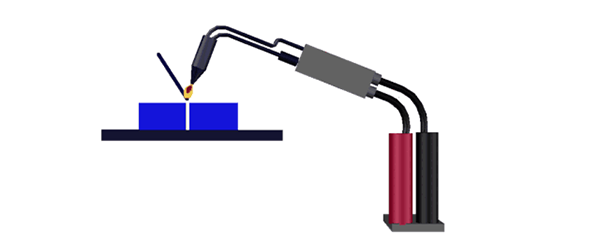
Шуудангийн цаг: 2024 оны 7-р сарын 29